I. Introduction
In the realm of industrial and commercial spaces, the role of shutter doors is pivotal, demanding precision and durability. The choice of materials in constructing shutter doors directly influences their performance, longevity, and overall quality. This comprehensive exploration aims to dissect the common materials used with shutter door machines and intricately examine how material selection significantly impacts the final product.
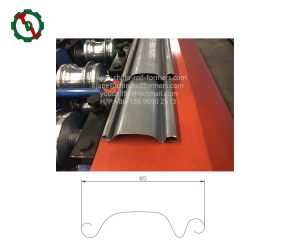
II. Common Materials for Shutter Door Machines
A. Galvanized Steel
- Overview:
Galvanized steel is a prevalent choice for shutter door manufacturing due to its inherent strength and corrosion resistance. The process of galvanization involves coating steel with a layer of zinc, providing a protective barrier against environmental elements.
- Impact on Final Product:
a. Durability: Shutter doors crafted from galvanized steel exhibit robust durability, ensuring a long lifespan even in challenging conditions.
b. Corrosion Resistance: The zinc coating protects against rust and corrosion, making galvanized steel shutter doors suitable for diverse environments.
B. Aluminum
- Overview:
Aluminum is favored for its lightweight nature and corrosion resistance. It is often chosen for applications where reduced weight and resistance to rust are critical factors.
- Impact on Final Product:
a. Weight Reduction: Shutter doors made from aluminum are lighter, facilitating smoother operation and potentially reducing the load on mechanical components. Shutter door machines, equipped with precise cutting and forming capabilities, ensure that the final product maintains the desired dimensions without compromising structural integrity.
b. Corrosion Resistance: Aluminum’s natural resistance to corrosion enhances the door’s longevity, making it suitable for outdoor applications.
C. Stainless Steel
- Overview:
Stainless steel is prized for its exceptional strength, aesthetic appeal, and resistance to corrosion. It is a common choice for applications where both functionality and visual appeal are paramount.
- Impact on Final Product:
a. Strength and Durability: Stainless steel shutter doors boast high strength, ensuring security and longevity.
b. Aesthetic Appeal: The polished finish of stainless steel contributes to a sleek and modern appearance, making it suitable for various architectural styles.
D. PVC (Polyvinyl Chloride)
- Overview:
PVC is a synthetic plastic material known for its versatility and cost-effectiveness. It is often used in the manufacturing of lightweight shutter doors.
- Impact on Final Product:
a. Affordability: PVC emerges as a cost-effective alternative in the construction of shutter doors. Leveraging the capabilities of a shutter door machine, PVC allows for budget-conscious projects without compromising on essential qualities.
b. Insulation Properties: PVC provides insulation, contributing to energy efficiency in spaces where temperature control is essential.
E. Composite Materials
- Overview:
Composite materials, combining different elements, are increasingly used in shutter door manufacturing to leverage the strengths of multiple materials.
- Impact on Final Product:
a. Tailored Performance: Composite materials allow for a customized approach, blending properties such as strength, insulation, and corrosion resistance to meet specific requirements.
b. Innovation: The use of composites enables the creation of shutter doors with unique characteristics, pushing the boundaries of design and functionality.
III. Considerations in Material Selection for Shutter Door Machine
A. Functional Requirements
Security: Depending on the application, materials must be chosen for the roller shutter machine to provide the required level of security and protection. Insulation: For spaces where temperature control is crucial, selecting materials with insulating properties becomes essential for the roller shutter machine.
B. Environmental Conditions
Outdoor Exposure: Shutter door machine materials must withstand exposure to varying weather conditions, including rain, sun, and temperature fluctuations. Chemical Exposure: In industrial settings, resistance to chemicals and pollutants may be a critical consideration for the roller shutter machine.
C. Cost Considerations
Budget Constraints: Project budgets play a crucial role in determining the feasibility of using certain materials for the roller shutter machine. Long-Term Cost Analysis: While some materials for the roller shutter machine may have higher initial costs, their long-term durability and low maintenance requirements may make them more cost-effective over time.
IV. Impact on the Manufacturing Process
The impact of shutter door machines on the manufacturing process is substantial, revolutionizing efficiency, precision, and customization in producing high-quality shutter doors. These machines play a pivotal role in shaping the modern manufacturing landscape, offering a range of benefits that enhance productivity and product quality. From automated processes to versatile design capabilities, the influence of roller shutter machines is evident in every stage of production.
- Precision and Consistency: Roller door machines bring a high degree of precision to the manufacturing process. Automated cutting, bending, and forming ensure consistency in dimensions and specifications. This precision is vital for creating shutter doors that fit seamlessly into diverse architectural and industrial settings.
- Increased Efficiency: The automation of key manufacturing steps significantly improves efficiency. Shutter door machines streamline processes, reducing manual labor and minimizing the margin for error. This efficiency not only accelerates production but also contributes to cost savings and overall operational excellence.
- Versatility in Design: Modern rolling roller door machines offer a remarkable level of versatility in design. From diverse material options to customizable patterns and features, these machines empower manufacturers to meet varied customer demands. The ability to create bespoke shutter doors enhances market competitiveness and customer satisfaction.
- Advanced Material Utilization: Shutter door machines optimize material usage, minimizing waste and maximizing resource efficiency. Computer-controlled processes ensure accurate measurements and cuts, reducing material costs and promoting sustainability in manufacturing practices.
- Enhanced Durability and Strength: The precision afforded by rolling roller door machines extends to the structural integrity of the doors. Consistent, accurate manufacturing results in shutter doors that boast enhanced durability and strength, meeting or exceeding industry standards for performance and longevity.
- Customization for Specialized Applications: Industries often require shutter doors tailored to specific needs, such as security, insulation, or weather resistance. Roller shutter machines enable the customization of doors to meet these specialized requirements, expanding the range of applications for these products.
- Integration of Smart Technologies: In line with industry 4.0 trends, modern rolling roller door machines integrate smart technologies for enhanced monitoring, control, and data analysis. This connectivity allows manufacturers to optimize production processes, predict maintenance needs, and adapt quickly to changing market demands.
- Adaptability to Market Trends: Shutter door machines enable manufacturers to stay agile and responsive to evolving market trends. Whether incorporating new materials, design aesthetics, or technological features, these machines provide the flexibility needed to align products with contemporary consumer preferences.
V. Future Trends and Innovations
A. Smart Materials Integration
- Overview:
The integration of smart materials, responsive to environmental conditions or user input, represents a cutting-edge trend in shutter door manufacturing.
- Impact on Final Product:
a. Enhanced Functionality: Smart materials can offer features such as self-healing, adaptive insulation, or integrated sensors for improved security and automation.
B. Sustainable Materials
- Overview:
With the escalating environmental consciousness, integrating sustainable materials into shutter door machine construction gains prominence. The conscientious choice of materials not only aligns with eco-friendly building practices but also addresses the evolving demands of regulatory compliance.
- Impact on Final Product:
a. Reduced Environmental Impact: Shutter doors manufactured using sustainable materials not only uphold ecological responsibility but also mitigate the environmental footprint associated with the operation of roller shutter machines.
b. Regulatory Compliance: The incorporation of sustainable materials in the shutter door machine aligns with stringent environmental standards, positioning manufacturers to meet evolving regulatory requirements and ensuring a responsible approach to production.
C. 3D Printing Technology
- Overview:
Advancements in 3D printing technology allow for the creation of intricate and customized shutter door components using various materials.
- Impact on Final Product:
a. Design Flexibility: 3D printing enables the production of complex geometries, providing opportunities for innovative and customized shutter door designs.
b. Material Diversity: 3D printing allows for experimentation with a wide range of materials, opening doors to new possibilities in shutter door construction.
VI. Conclusion
In conclusion, the choice of materials in shutter door manufacturing, guided by functional requirements, environmental conditions, and cost considerations, significantly influences the final product’s performance and longevity. Shutter door machines, particularly rolling roller door machines, play a pivotal role in revolutionizing the manufacturing process, enhancing precision, efficiency, and customization. Their impact includes increased versatility in design, advanced material utilization, and integration of smart technologies. Future trends highlight the integration of smart and sustainable materials, as well as advancements in 3D printing technology. Case studies exemplify application-specific material choices, such as galvanized steel for industrial warehouses and aluminum for commercial storefronts. Performance monitoring and comparative analysis contribute to informed material selection strategies, ensuring the continuous evolution of shutter door manufacturing practices.