Introduction
Crimping curving machines are essential tools in the metalworking and construction industries, used to shape and form metal sheets into curved profiles. These machines are highly valued for their precision, efficiency, and versatility. Understanding the operation of a crimping curving machine is crucial for professionals in the field, as it ensures optimal use and maintenance. This article will delve into the detailed operation of these machines, exploring their components, working principles, and applications.
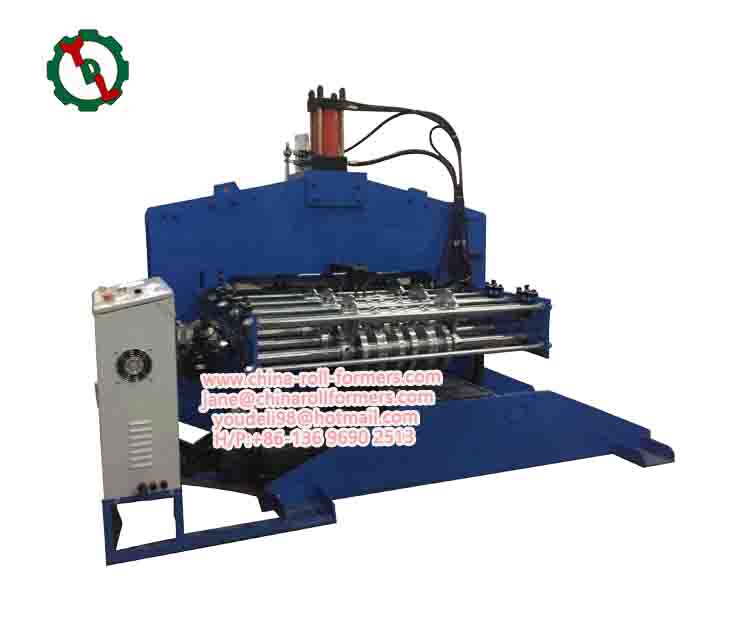
1. Overview of Crimping Curving Machines
- Definition and Purpose
It is designed to create curved or crimped profiles on metal sheets, which are commonly used in roofing, cladding, and various architectural applications.
The machine operates by feeding metal sheets through a series of rollers and dies, which progressively shape the metal into the desired curved profile.
- Types of Crimping Curving Machines
Manual: Operated by hand, suitable for small-scale projects or when precision is not the primary concern.
Automatic: Equipped with advanced control systems, suitable for large-scale production with high precision requirements.
2. Key Components of a Crimping Curving Machine
- Frame
The sturdy frame of the machine supports all other components and ensures stability during operation. It is usually made of high-strength steel to withstand the forces involved in crimping and curving.
- Rollers and Dies
Rollers: Multiple sets of rollers progressively shape the metal sheet as it passes through the machine. The rollers can be adjusted to accommodate different metal thicknesses and curvature requirements.
Dies: Specialized dies are used to create specific crimp patterns on the metal sheet. These dies can be interchanged to produce different profiles.
- Feeding Mechanism
The feeding mechanism ensures the smooth and continuous movement of the metal sheet through the machine. It can be powered by electric motors or manually operated, depending on the machine type.
- Control System
Modern crimping curving machines are equipped with computerized control systems that allow precise adjustments to the rollers and dies. These systems can store multiple profiles and settings for quick changeovers between different production runs.
3. Working Principles of a Crimping Curving Machine
- Preparation and Setup
Before operating the machine, the operator must prepare the metal sheets and set up the machine according to the desired profile. This includes adjusting the rollers and dies, setting the feeding speed, and configuring the control system.
- Feeding the Metal Sheet
The metal sheet is fed into the machine through the feeding mechanism. The feeding speed can be adjusted based on the material type and thickness to ensure optimal shaping and minimize deformation.
- Crimping and Curving Process
As the metal sheet passes through the rollers and dies, it undergoes a series of gradual deformations. The rollers apply pressure to the sheet, bending it into the desired curvature while the dies create the crimp pattern.
The process involves multiple stages, with each set of rollers and dies performing a specific function. The gradual deformation ensures smooth curves and prevents the metal from cracking or breaking.
- Output and Quality Control
Once the metal sheet has passed through all the rollers and dies, it emerges with the final curved and crimped profile. The operator must inspect the output to ensure it meets the required specifications.
Modern machines often include quality control systems that automatically detect defects and adjust the machine settings to maintain consistent quality.
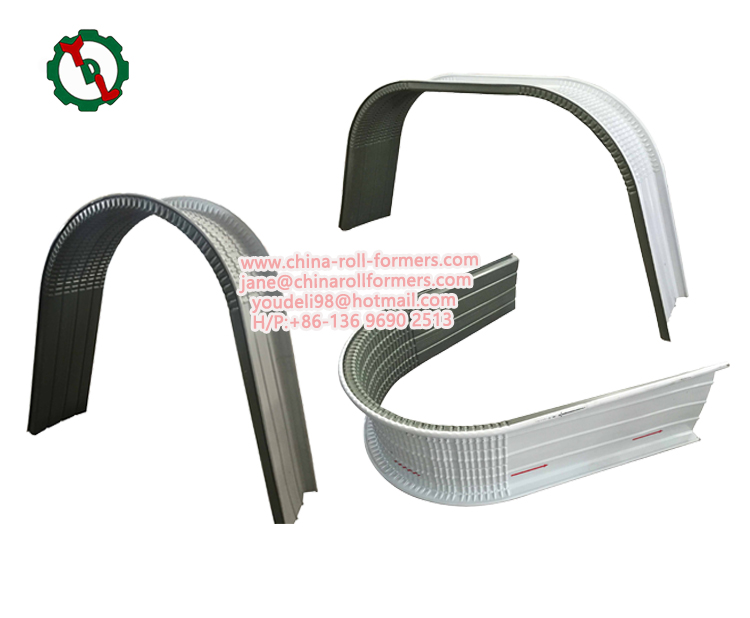
4. Applications of Crimping Curving Machines
- Roofing and Cladding
They are widely used in the production of metal roofing and cladding panels. The curved profiles enhance the aesthetic appeal and provide better structural integrity.
- Architectural Design
In architectural design, crimped and curved metal sheets are used to create unique facades, canopies, and other decorative elements. The versatility of these machines allows for the production of complex and customized profiles.
- Industrial Components
They are also used in the production of industrial components such as ducts, pipes, and structural supports. The machines ensure precise and consistent shapes, which are crucial for these applications.
- Automotive Industry
In the automotive industry, they are used to manufacture body panels and other metal components. The ability to create precise curves and crimps is essential for maintaining the aerodynamic properties and structural integrity of vehicles.
5. Maintenance and Safety Considerations
- Regular Maintenance
To ensure the longevity and optimal performance of it, regular maintenance is essential. This includes lubricating moving parts, checking for wear and tear, and replacing worn-out components.
Scheduled maintenance should be performed according to the manufacturer’s guidelines, and any issues should be addressed promptly to prevent machine downtime.
- Safety Measures
Operating a crimping curving machine involves significant risks, and proper safety measures must be in place. Operators should receive comprehensive training and follow safety protocols, such as wearing protective gear and ensuring the machine is properly grounded.
Modern machines are equipped with safety features such as emergency stop buttons, safety guards, and automatic shutoff systems to protect operators from accidents.
6. Advancements in Crimping Curving Machine Technology
- Automation and Control
Recent advancements in automation and control systems have significantly improved the efficiency and precision of it Computerized controls allow for quick adjustments and the ability to store multiple profiles for easy changeovers.
Automation reduces the need for manual intervention, minimizing human error and increasing production speed.
- Material Handling and Feeding Systems
Improved material handling and feeding systems ensure smooth and continuous operation, reducing the risk of material jams and inconsistencies. These systems can handle a wide range of metal types and thicknesses, enhancing the machine’s versatility.
- Energy Efficiency
Modern crimping curving machines are designed with energy efficiency in mind. Advanced motor technologies and optimized mechanical designs reduce energy consumption, making the machines more environmentally friendly and cost-effective.
Conclusion
Crimping curving machines are indispensable tools in the metalworking and construction industries, providing the ability to create precise and aesthetically pleasing curved metal profiles. Understanding the operation of these machines, from the key components to the working principles and applications, is crucial for professionals in the field. Regular maintenance and adherence to safety protocols ensure the longevity and safe operation of the machines. With continuous advancements in technology, they are becoming more efficient, versatile, and user-friendly, further expanding their applications in various industries.