Sandwich panels, composed of two outer metal sheets with insulating core material, are widely used in the construction of buildings and facilities for their excellent thermal insulation, lightweight, and high strength. The sandwich panel roll forming machine plays a crucial role in the manufacturing of these panels, providing an efficient, automated solution for producing high-quality sandwich panels at scale. This article delves into the workings of a sandwich panel roll forming machine, covering its design, components, operation, and the benefits it brings to the construction materials industry.
Introduction to Sandwich Panel Roll Forming Machines
A sandwich panel roll forming machine is a specialized piece of equipment designed to produce sandwich panels. These machines are highly sought after in the construction industry due to their capability to manufacture panels that meet various structural and insulation requirements. The core materials typically used in sandwich panels include polyurethane (PU), polyisocyanurate (PIR), mineral wool, and expanded polystyrene (EPS), each offering different levels of thermal insulation, fire resistance, and weight.
Components of the Machine
The machine consists of several key components:
- Uncoiler: This part holds and feeds the outer metal sheets into the machine. It is crucial for maintaining the material’s tension and alignment throughout the production process.
- Roll Forming Section: Here, the metal sheets are gradually formed into the desired profile through a series of rolls. This section is critical for ensuring the structural integrity and aesthetic appeal of the outer layers.
- Core Material Injection: In this stage, the core material is injected or placed between the two metal sheets. For foam cores like PU or PIR, a high-pressure injection system is used, whereas for solid cores like EPS or mineral wool, the material is manually or automatically fed into the assembly.
- Laminating and Pressing Section: This part of the machine applies pressure and sometimes heat to bond the metal sheets to the core material, ensuring a strong, uniform adhesion across the panel.
- Cutting Section: Once the sandwich panel is formed, it is cut into predetermined lengths according to the project requirements.
- Control System: The entire operation is managed and monitored through a sophisticated control system, which ensures precision in the production process and allows for adjustments to be made on the fly.
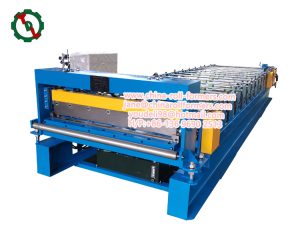
How the Machine Works
The manufacturing process begins with the uncoiling of the metal sheets, which are then fed into the roll forming section. Here, the sheets are shaped into the correct profile through a series of rolls. The profiles formed depend on the specific application of the sandwich panel, ranging from flat sheets for walls to corrugated profiles for roofing.
Once the metal sheets have been formed, the core material is introduced. In the case of liquid foams like PU or PIR, the two components of the foam are mixed and injected between the sheets under high pressure. This mixture then expands and cures to form a rigid insulating layer. For solid cores, the sheets are brought together with the core material already in place.
The laminating and pressing section is where the composite structure is bonded together. For foam cores, the exothermic reaction of the curing process helps to bond the core to the metal sheets. Additional heat and pressure may be applied to ensure a strong bond. For solid cores, adhesives may be used, and pressure is applied to ensure a uniform bond across the panel.
Finally, the continuous sandwich panel is cut to the desired length, inspected for quality, and then stacked or packaged for shipping.
Advantages of Using a Sandwich Panel Roll Forming Machine
The use of a sandwich panel roll forming machine offers numerous benefits to manufacturers:
- Efficiency: The automated nature of the machine allows for continuous production, significantly reducing manufacturing times and increasing output.
- Consistency: The controlled process ensures that each panel produced meets strict quality standards, providing consistent insulation properties and structural integrity.
- Flexibility: Modern machines can be adjusted to produce panels of different sizes, thicknesses, and various core materials, allowing manufacturers to cater to a wide range of market demands.
- Cost-effectiveness: The automation and speed of production reduce labor costs and material wastage, making the manufacturing process more economical.
Technological Advancements in Sandwich Panel Roll Forming Machines
The evolution of sandwich panel roll forming machines has been driven by the need for greater efficiency, versatility, and precision in the production of sandwich panels. Some of the latest technological advancements in these machines include:
- Automated Core Material Handling: Modern machines are equipped with automated systems for handling core materials, such as robotic arms for placing solid cores or advanced injection systems for foam cores. This automation enhances production speed and reduces manual labor.
- Integrated Cutting Systems: Cutting systems have become more sophisticated, with the ability to make precise cuts at high speeds, ensuring panels are cut to exact specifications without slowing down the production process.
- Advanced Control Systems: The use of PLCs (Programmable Logic Controllers) and touchscreen interfaces has improved the control and monitoring of the production process, allowing for real-time adjustments and diagnostics.
- Customization Capabilities: New machines offer greater flexibility in terms of panel profiles, sizes, and core materials, enabling manufacturers to produce panels tailored to specific project requirements.
- Energy Efficiency: Advances in machine design and operation have led to reduced energy consumption, making the production process more sustainable and cost-effective.
Challenges and Future Outlook
Despite the numerous advantages, there are challenges that manufacturers face when using sandwich panel roll forming machines. These include the initial high investment cost, the need for regular maintenance to ensure optimal performance, and the requirement for skilled operators to manage the complex machinery.
Looking ahead, the future of sandwich panel roll forming machines is likely to be shaped by further technological innovations, such as the integration of artificial intelligence for predictive maintenance and optimization, the use of more sustainable materials, and the development of even more versatile and efficient machines. As the demand for energy-efficient and high-strength building materials continues to grow, sandwich panel forming machines will remain an essential tool in the construction industry’s arsenal.
Conclusion
Sandwich panel roll forming machines have revolutionized the production of sandwich panels, offering a highly efficient, consistent, and flexible manufacturing solution. As technology continues to advance, these machines will evolve to meet the ever-changing demands of the construction industry, ensuring that sandwich panels remain a key component in modern building design and construction.
It is a cornerstone of modern construction materials manufacturing, enabling the production of high-quality, durable, and energy-efficient panels. Its sophisticated design and operation facilitate the efficient production of panels that meet the exacting standards of today’s construction industry. As technology advances, these machines continue to evolve, offering even greater efficiency, flexibility, and reliability, thereby ensuring that sandwich panels remain a preferred choice for builders and architects around the globe.