I. Introduction
Roll forming is a manufacturing process used to shape metal sheets into desired cross-section profiles. It involves passing a continuous strip of metal through a series of rollers to gradually bend the metal into the desired shape. This process is widely used in various industries, including automotive, construction, and appliance manufacturing, due to its efficiency and versatility.
Custom roll forming machines play a crucial role in enhancing manufacturing processes by allowing companies to create complex and customized metal profiles with high precision and consistency. These machines can be tailored to meet specific production requirements, making them ideal for producing a wide range of products, from simple channels to intricate trim components. They are designed to increase productivity, reduce waste, and improve overall product quality, making them a valuable asset in modern manufacturing operations.
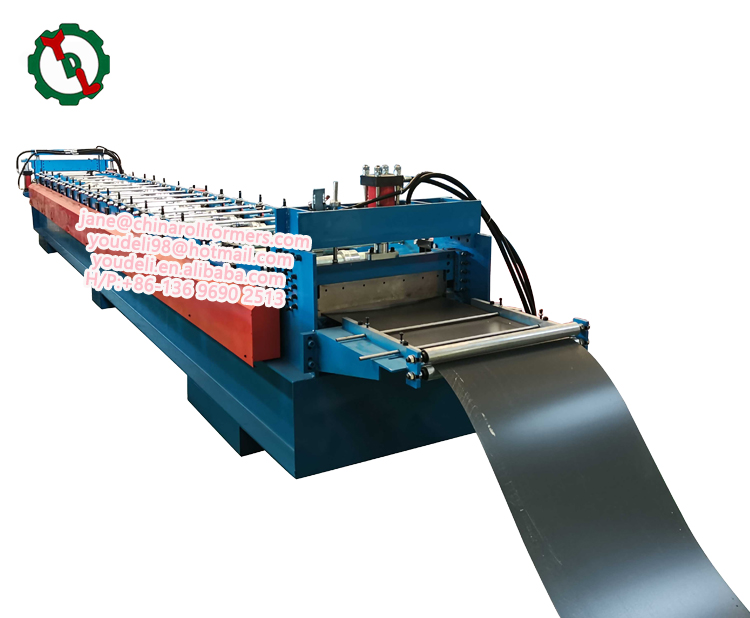
II. Cost Efficiency
Custom roll forming machines play a crucial role in enhancing cost efficiency in manufacturing processes. Here’s how:
- Reduced Material Waste: They are designed to precisely shape metal coils into the desired profiles. This precision ensures minimal material waste compared to traditional methods like cutting and welding. The ability to produce complex shapes without excess material leads to significant cost savings over time.
- Efficient Production Process: Custom roll forming machines are highly efficient, capable of running at high speeds while maintaining accuracy and consistency. This efficiency translates to lower production costs by reducing labor requirements and energy consumption per unit produced.
- Lower Labor Costs: Automated roll forming machines require fewer operators compared to manual or less automated processes. This reduction in labor costs contributes to overall cost efficiency in manufacturing.
- Economies of Scale: They are well-suited for high-volume production runs. The ability to produce large quantities of consistent, high-quality parts in a short period allows manufacturers to take advantage of economies of scale, further reducing production costs per unit.
- Minimal Tooling Costs: Once a custom roll forming machine is set up and running, the costs associated with tooling are relatively low. This is especially beneficial for long production runs, as the initial tooling costs can be amortized over a larger number of units, reducing the cost per unit produced.
They offer significant cost efficiency benefits by reducing material waste, optimizing production processes, lowering labor costs, enabling economies of scale, and minimizing tooling costs. Integrating these machines into manufacturing operations can lead to substantial savings and improved profitability.
III. Flexibility and Versatility
Flexibility and versatility are key attributes of custom roll forming machines, allowing them to be tailored to specific product requirements. These machines can be customized in various ways, such as adjusting the number and configuration of rolls, changing the speed and pressure of the forming process, and incorporating specialized tooling and accessories. This customization enables manufacturers to produce a wide range of shapes and sizes, from simple profiles to complex geometries, with precision and efficiency. Additionally, the modular nature of custom roll forming machines allows for easy reconfiguration and adaptation to accommodate changing production needs, making them an ideal solution for manufacturers seeking flexibility in their manufacturing processes.
IV. Consistency and Quality
Custom roll forming machines play a crucial role in ensuring consistent product quality in manufacturing processes. These machines are designed to meet specific production requirements, resulting in a level of precision and accuracy that is unmatched by standard machines.
One key aspect of it is their ability to maintain consistent material thickness and shape throughout the production process. This consistency is essential for ensuring that each piece meets the required specifications and performs as intended once installed.
Additionally, they allow for greater control over the manufacturing process, leading to improved quality control measures. Manufacturers can monitor and adjust various parameters, such as speed, pressure, and temperature, to ensure that each piece meets the desired quality standards.
The precision and accuracy achieved through customization are critical for meeting the demanding requirements of modern industries. Whether producing complex profiles or standard shapes, custom roll forming machines enable manufacturers to achieve the highest levels of consistency and quality in their products.
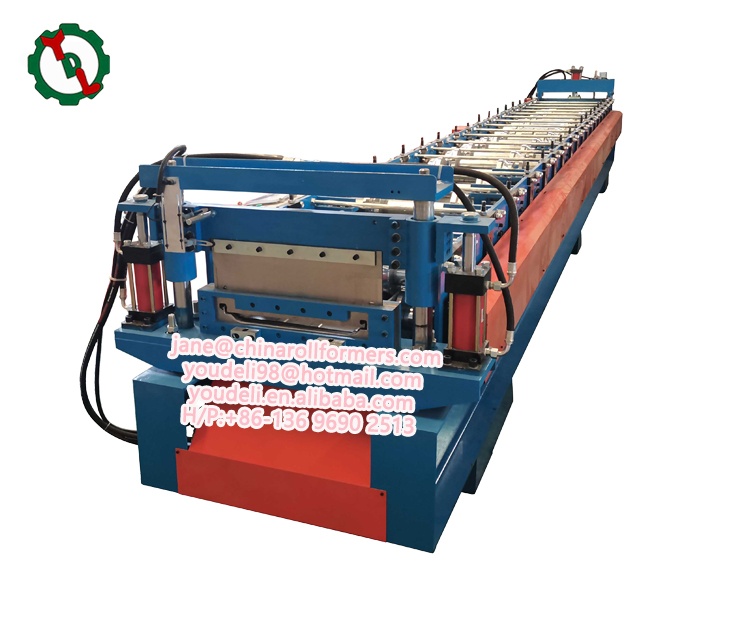
V. Increased Production Speed
Custom roll forming machines play a crucial role in enhancing production speed compared to manual or traditional methods. These machines are designed to efficiently and accurately shape metal coils into desired profiles, allowing for rapid and continuous production. Here’s how they contribute to increased production speed:
- Automated Process: They are automated, reducing the need for manual intervention. This automation ensures consistent production speed and eliminates the variability associated with manual labor, leading to higher efficiency.
- High-Speed Operation: These machines are capable of operating at high speeds, significantly increasing the output compared to manual methods. They can continuously produce formed metal parts at a rapid pace, thereby boosting overall production speed.
- Quick Setup and Changeover: They are designed for quick setup and changeover between different profiles. This feature reduces downtime between production runs, allowing for more efficient use of time and resources.
- Precision and Accuracy: The precise nature of custom roll forming machines ensures that each formed part meets the required specifications. This eliminates the need for rework or corrections, further enhancing production speed.
They play a crucial role in increasing production speed and overall manufacturing efficiency. Their ability to automate and accelerate the forming process results in higher output, reduced lead times, cost savings, and improved resource utilization, making them an indispensable tool for modern manufacturing processes.
VI. Adaptability to Industry Requirements
Custom roll forming machines play a crucial role in meeting specific industry standards and regulations by offering adaptability and flexibility in their design and operation. These machines can be customized to produce profiles that meet the exact specifications required by different industries, ensuring compliance with regulatory standards and quality requirements.
In the construction industry, for example, they can be tailored to produce steel profiles that meet structural integrity and durability standards. This adaptability allows construction companies to use these profiles confidently in their projects, knowing they meet or exceed industry regulations.
Similarly, in the automotive industry, they can be adapted to produce complex shapes and profiles used in vehicle chassis and body structures. This adaptability ensures that these components meet stringent safety and performance standards required in the automotive sector.
In the aerospace industry, where precision and quality are paramount, they can be customized to produce aerospace-grade profiles with tight tolerances and high-quality finishes. This adaptability ensures that these profiles meet the rigorous standards set by the aerospace industry for safety and performance.
Overall, the adaptability of custom roll forming machines is crucial in various industries such as construction, automotive, and aerospace, as it allows manufacturers to produce profiles that meet specific industry requirements and regulations, ensuring the quality and safety of their products.
VII. Conclusion
The utilization of a custom roll forming machine for manufacturing offers a multitude of advantages. These machines provide precise and consistent shaping of metal materials, ensuring high-quality end products. They also offer versatility, allowing for the creation of complex profiles and shapes to meet specific design requirements. Furthermore, they enhance efficiency and productivity by streamlining the manufacturing process and reducing waste.
The potential of these machines to revolutionize the manufacturing process in various industries is significant. They can expedite production timelines, reduce production costs, and improve overall product quality. Additionally, the ability to create custom profiles and shapes opens up new possibilities for product innovation and design.
Overall, the adoption of custom roll forming machines represents a strategic investment for manufacturers looking to enhance their capabilities, improve their competitiveness, and drive innovation in their respective industries.