Introduction
A sandwich panel roll forming machine is a highly specialized piece of equipment designed to produce sandwich panels, which are widely used in construction for their excellent insulation properties and structural strength. These machines are integral to the manufacturing process of sandwich panels, which consist of a core material sandwiched between two layers of metal or other rigid materials. It ensures precision, efficiency, and quality when producing these panels. This article explores the main features of a sandwich panel roll forming machine, emphasizing its technical aspects, operational efficiency, and benefits.
1. Precision Engineering and Design
The sandwich panel roll forming machine is designed with high-precision engineering to ensure the accurate shaping and alignment of the panels. Key components contributing to this precision include:
- Rollers and Molds: The machine features a series of rollers and molds that shape the metal sheets and core material into the desired panel configuration. These rollers are made from high-quality steel and are precisely machined to maintain consistent dimensions.
- Adjustable Rollers: The rollers are adjustable to accommodate different panel thicknesses and profiles, allowing for versatility in panel design.
- Cutting System: An integrated cutting system precisely cuts the panels to the required lengths. This system is often controlled by CNC (Computer Numerical Control) technology for enhanced accuracy.
2. Automation and Control Systems
Modern sandwich panel roll forming machines are equipped with advanced automation and control systems that enhance their efficiency and ease of use. These systems include:
- PLC Control: A Programmable Logic Controller (PLC) manages the machine’s operations, ensuring precise control over the roll forming process. The PLC can be programmed to produce panels of various sizes and configurations.
- HMI Interface: A Human-Machine Interface (HMI) allows operators to easily input specifications, monitor the machine’s status, and make adjustments as needed. This interface simplifies the operation and reduces the potential for human error.
- Automated Material Feeding: Automated feeding systems ensure a continuous supply of materials into the machine, minimizing downtime and increasing productivity.
3. High Production Speed
One of the standout features of a sandwich panel roll forming machine is its high production speed. These machines are designed to produce large quantities of panels quickly and efficiently. Factors contributing to this high speed include:
- Continuous Operation: The machine operates continuously, with materials fed in at one end and finished panels exiting at the other. This continuous process eliminates the need for frequent stops and starts.
- High-Speed Rollers: The rollers operate at high speeds, rapidly shaping the materials into the desired panel configuration.
- Efficient Cutting Mechanism: The cutting system works in tandem with the rollers to cut panels to the required lengths without slowing down the production line.
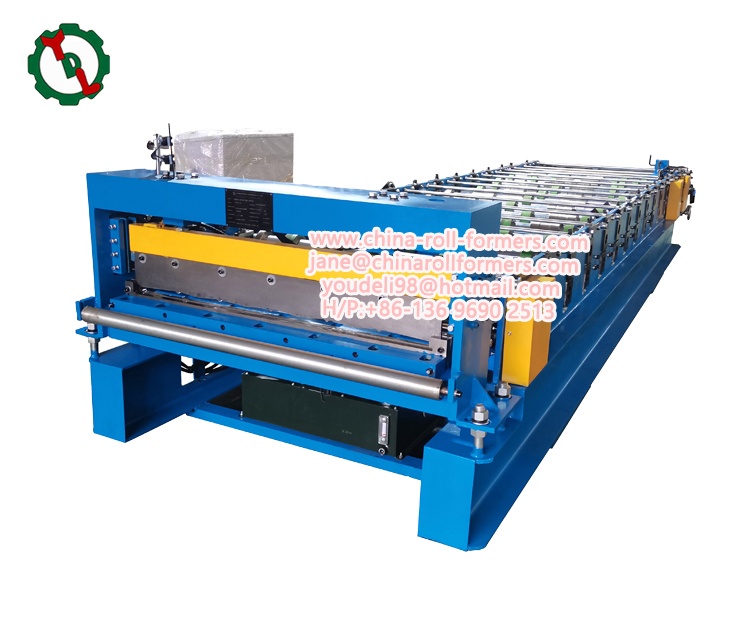
4. Versatility in Panel Design
A sandwich panel roll forming machine offers versatility in the design and production of different types of sandwich panels. This versatility is achieved through:
- Adjustable Rollers and Molds: The machine can be adjusted to produce panels with varying thicknesses, core materials, and profiles. This flexibility allows manufacturers to produce panels for different applications, such as walls, roofs, and floors.
- Customizable Configurations: Manufacturers can customize the machine to produce panels with specific properties, such as enhanced insulation or increased structural strength. This customization is facilitated by the machine’s modular design.
5. Durability and Longevity
The sandwich panel roll forming machine is built to withstand the rigors of continuous operation in an industrial setting. Key features that contribute to its durability and longevity include:
- Robust Construction: The machine is constructed from high-quality materials, including hardened steel for the rollers and frame. This robust construction ensures that the machine can handle heavy loads and resist wear and tear.
- Low Maintenance Requirements: The machine is designed for low maintenance, with features such as self-lubricating bearings and easy-to-replace components. This design minimizes downtime and reduces maintenance costs.
- Reliable Performance: The machine’s components are engineered for reliable performance, ensuring consistent quality and output over time.
6. Energy Efficiency
Energy efficiency is a significant consideration in the design of modern sandwich panel roll forming machines. These machines are equipped with features that minimize energy consumption, including:
- Energy-Efficient Motors: The motors used in the machine are designed for high efficiency, reducing energy consumption while maintaining high performance.
- Smart Power Management: The control systems include smart power management features that optimize energy use during operation. For example, the machine may automatically enter a low-power mode when not in use.
- Reduced Waste: The precision engineering of the machine minimizes material waste, which not only saves costs but also reduces the energy required to produce additional materials.
7. Safety Features
Safety is paramount in the operation of a sandwich panel roll forming machine. Modern machines are equipped with a range of safety features to protect operators and prevent accidents, including:
- Emergency Stop Buttons: Easily accessible emergency stop buttons allow operators to quickly halt the machine in case of an emergency.
- Safety Guards: The machine is fitted with safety guards to protect operators from moving parts and prevent accidental contact.
- Automatic Shutoff: The machine can be programmed to automatically shut off if it detects any irregularities or malfunctions, preventing damage and ensuring operator safety.
8. Integration with Other Equipment
A sandwich panel roll forming machine can be integrated with other equipment in a production line to enhance efficiency and streamline operations. This integration includes:
- Material Handling Systems: The machine can be connected to automated material handling systems, such as conveyors and feeders, to ensure a steady supply of materials.
- Quality Control Systems: Integration with quality control systems allows for real-time monitoring and inspection of panels, ensuring that each panel meets the required specifications.
- Packaging Systems: The machine can be linked to automated packaging systems, which package the finished panels for shipping and distribution.
9. Customization and Upgrades
Manufacturers can customize and upgrade their sandwich panel roll forming machines to meet specific production requirements. Customization options include:
- Specialized Rollers and Molds: Manufacturers can order specialized rollers and molds to produce panels with unique profiles or features.
- Additional Automation: Additional automation features, such as robotic arms or automated inspection systems, can be integrated into the machine to further enhance efficiency and precision.
- Software Upgrades: Software upgrades can improve the machine’s performance and add new functionalities, such as advanced diagnostic tools or enhanced control algorithms.
10. Cost-Effectiveness
Despite their advanced features and capabilities, sandwich panel roll forming machines are cost-effective investments for manufacturers. Key factors contributing to their cost-effectiveness include:
- High Production Output: The machine’s high production speed and efficiency result in a high output of panels, which translates to increased revenue and faster return on investment.
- Reduced Labor Costs: The automation and ease of operation of the machine reduce the need for manual labor, resulting in lower labor costs.
- Low Maintenance Costs: The machine’s durable construction and low maintenance requirements minimize downtime and reduce maintenance costs.
Conclusion
The sandwich panel roll forming machine is a vital piece of equipment in the production of sandwich panels, offering a range of features that enhance precision, efficiency, and versatility. With advanced automation and control systems, high production speeds, and robust construction, these machines are designed to meet the demands of modern manufacturing. Their energy efficiency, safety features, and integration capabilities make them a valuable investment for manufacturers looking to produce high-quality sandwich panels. Customization options and the potential for upgrades further enhance the machine’s appeal, ensuring that it can adapt to evolving production needs. Overall, the sandwich panel roll forming machine stands out as a cost-effective, reliable, and essential tool in the construction industry.