A curving machine, often found in industrial settings, is a piece of equipment designed to bend or curve metal sheets, tubes, or other materials into a desired shape or angle without compromising the material’s integrity or strength. This machinery plays a crucial role in various sectors, including automotive, aerospace, construction, and manufacturing, facilitating the creation of complex parts and structures. This article delves into the intricacies of curving machines, exploring their types, working principles, applications, and technological advancements enhancing their performance.
Types of Curving Machines
Curving machines come in various forms, each tailored to specific applications and materials. The primary types include:
- Plate Bending Machines: These machines are used to curve metal plates. They can range from simple, manual devices to highly sophisticated, CNC-controlled systems that can bend large, thick plates.
- Tube Bending Machines: These are designed to curve tubes and pipes. Depending on the tube’s diameter and wall thickness, these machines can be manually operated or fully automated.
- Section Bending Machines: These are used to bend profiles, such as beams, angles, and channels, into curves or rings. They are essential in creating frames and supports in construction and manufacturing.
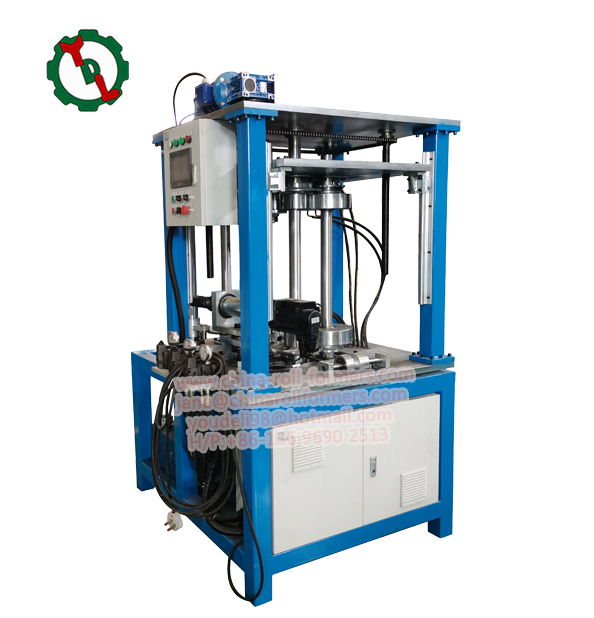
Working Principle
The working principle of a curving machine revolves around the application of force to bend or curve the material. The process involves three main components: the bending force, the material itself, and the machine’s mechanics. Here’s how it typically works:
- Material Placement: The raw material, such as a metal sheet or tube, is placed between dies or rollers, depending on the machine’s design.
- Force Application: The machine applies force to the material, causing it to bend around the die or rollers. In manual machines, this force is applied through a lever or handle, while hydraulic or pneumatic systems power more advanced machines.
- Precision Shaping: For high-precision curving, CNC (Computer Numerical Control) machines are used, where the bending process is controlled by computerized systems ensuring accuracy and repeatability.
Applications of Curving Machines
They have a wide range of applications across various industries:
- Automotive Industry: Used in manufacturing car frames, exhaust pipes, and other curved metal parts.
- Construction: Essential for creating curved beams, arches, and frames used in buildings, bridges, and other structures.
- Aerospace: Used to form structural components of aircraft and spacecraft that require precise curvatures.
- Furniture Manufacturing: In crafting metal frames for chairs, tables, and decorative items.
Technological Advancements
Technological advancements have significantly impacted the development and efficiency of curving machines. Some notable improvements include:
- CNC Technology: Computer-controlled bending machines offer unparalleled precision and speed, allowing for complex shapes and designs that would be difficult or impossible to achieve manually.
- Hydraulic and Pneumatic Systems: These systems provide more power and control compared to manual operations, enabling the bending of thicker and harder materials.
- Automated Material Handling: Integration with robotic systems for material feeding and handling streamlines the bending process, reducing labor costs and improving safety.
Challenges and Solutions
Operating curving machines, especially for complex or large-scale projects, can present several challenges:
- Material Springback: After bending, materials tend to return slightly to their original shape, a phenomenon known as springback. Addressing this requires precise control of the bending angle and continuous monitoring during the process.
- Tooling Wear: Frequent use can wear down the dies and rollers, affecting the machine’s performance. Regular maintenance and using high-quality tooling materials can mitigate this issue.
- Complexity of Designs: As designs become more complex, the need for sophisticated machines with advanced programming capabilities increases. Investing in CNC technology and skilled operators is essential for handling intricate projects.
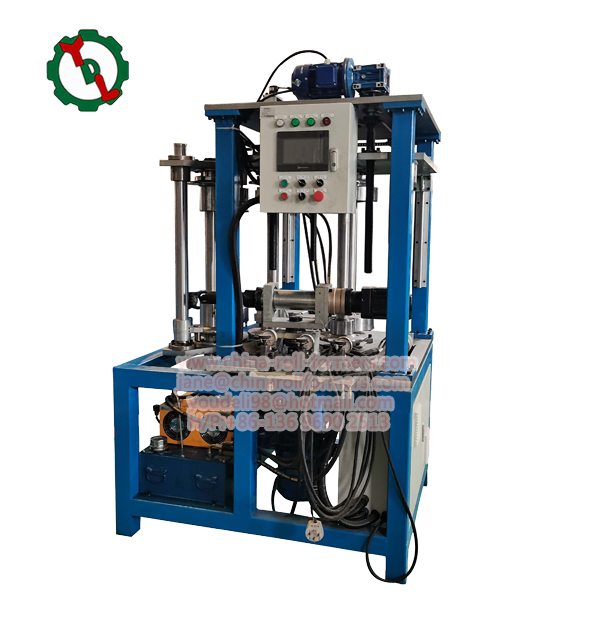
Maintenance and Safety
Proper maintenance and adherence to safety protocols are paramount in ensuring the efficiency and longevity of it:
- Regular Maintenance: Routine checks and servicing help prevent breakdowns and extend the machine’s lifespan. This includes lubricating moving parts, checking hydraulic systems, and replacing worn components.
- Operator Training: Operators must be adequately trained in machine operation and safety procedures to prevent accidents and ensure smooth operation.
- Safety Measures: Implementing safety measures, such as emergency stop buttons, guards, and warning signals, helps minimize the risk of injuries and accidents.
Considerations for Choosing a Curving Machine
Selecting the appropriate bending machine for a specific application requires careful consideration of several factors:
- Material Compatibility: Different machines are optimized for various materials and thicknesses. It is crucial to choose a machine that can effectively handle the specific material you intend to curve.
- Capacity and Size: The size and bending capacity of the machine should match the scale of the projects it will be used for. Larger, industrial-grade machines are necessary for bending thick plates or large tubes, whereas smaller projects might only require a manual or benchtop model.
- Flexibility and Versatility: For operations that involve a variety of bending tasks, machines with adjustable settings and the ability to handle multiple types and sizes of materials are preferable.
- Cost Efficiency: The machine’s cost should align with the budget and expected ROI. This includes not only the initial purchase price but also long-term costs related to maintenance, operation, and tooling replacements.
Future Outlook and Trends
The future of curving machines looks promising, with several trends shaping their evolution:
- Automation and Robotics: The integration of automation and robotics with these is set to increase efficiency and reduce the need for manual labor, especially in repetitive or high-volume bending tasks.
- Advanced Materials: As new materials with improved properties are developed, these will need to adapt to handle these innovations, necessitating advancements in machine design and capabilities.
- Sustainability: With an increasing focus on sustainability, there is a push towards energy-efficient machines and processes that minimize waste and reduce the environmental impact of manufacturing operations.
- Digitalization and IoT: The adoption of digital technologies and the Internet of Things (IoT) in these allows for better monitoring, predictive maintenance, and optimization of the bending process, enhancing overall productivity and reliability.
Conclusion
Curving machines are indispensable tools in the arsenal of modern manufacturing and construction, enabling the production of essential components with high precision and efficiency. As industries continue to evolve, the demand for more advanced, versatile, and sustainable bending machines is expected to grow. By understanding the fundamentals, applications, and future directions of this technology, companies can make informed decisions that align with their operational needs and strategic goals. With ongoing advancements in automation, materials science, and digital technologies, the capabilities and applications of curving machines will undoubtedly expand, offering new opportunities for innovation and efficiency in manufacturing processes.